| China
Qingdao Float Glass Co.,Ltd
Qingdao Rolled Glass Co.,Ltd
TG Changjiang Co.,Ltd
Taichia Glass Fiber Co.,Ltd
TG Chengdu Glass Co.,Ltd
TG Huanan Glass Co.,Ltd
TG Donghai Glass Co., Ltd.
TG Kunshan Glass Co.,Ltd
TG Tianjin Glass.Co.,Ltd
Taichia Chengdu Glass Fiber Co.,Ltd
|
|
|
|
|
|
|
|
Factory Land |
126,552m2 |
Building Area |
84,609m2 |
Furnaces |
7 |
Process Lines |
Printing |
Capacity |
177,800MT |
|
|
Production |
container glass Tableware glass kitchenware glass Rolled Glass |
|
 |
 |
 |
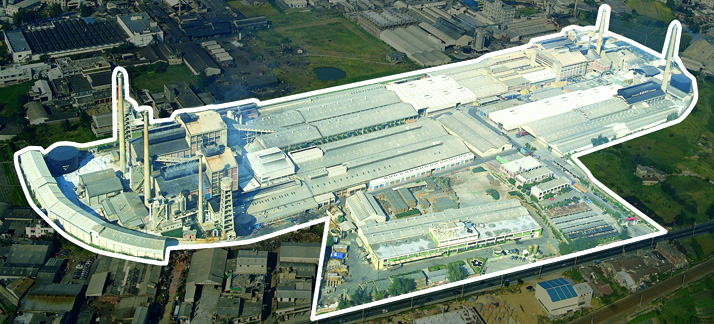 |
|
Taiwan Glass's Hsinchu plant was established in 1965, and is Taiwan Glass's first factory. Since it fired up its kilns and began production in 1967, this plant has continuously acquired advanced domestic and foreign advanced technology, and has collaborated with other well-known glass producers worldwide. The plant has variously produced patterned glass, container glass, food and beverage vessel glass, and heat-resistant glass, and wrote many chapters in Taiwan Glass's development into a prominent international glass group.
|
|
.jpg) |
|
The Hsinchu plant's main product is container glass. The plan has engaged in technological collaboration with America's Wheaton Glass, Germany's Veba Glass, and Japan's Yamamura Glass since it began operation in 1969, and acquired NNPB glass blowing technology from Germany's Heye Glass. By manufacturing lightweight bottles with even thickness, we help customers cut costs and energy losses. To better meet customers' needs, we have continued to develop colored bottles in recent years. |
|
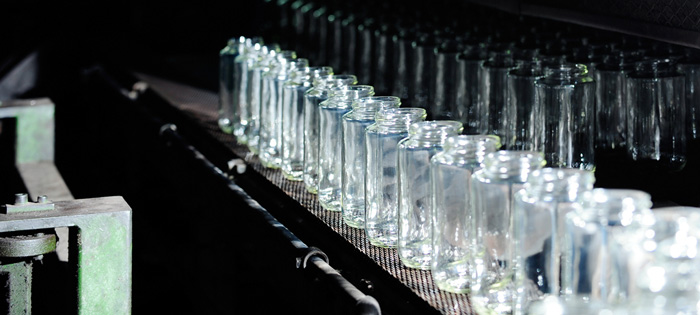 |
|
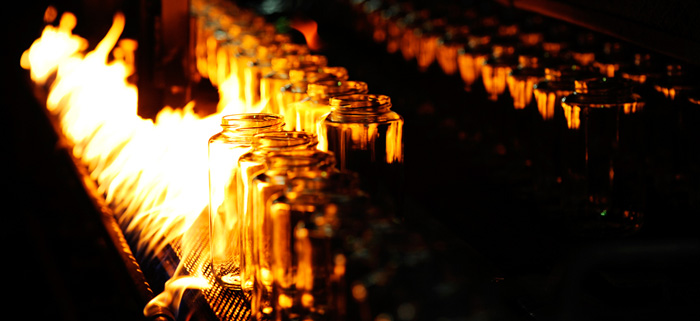 |
|
We acquired blowing and pressing technology and for good and beverage vessels from Germany's VEBA in 1977. To date, we have manufactured more than a hundred kinds of cups, plates, and bowls, etc., and we continue to develop new products. In conjunction with our adoption of six-color printing technology and colorful packaging box design, we have now completed investment in equipment for producing colored glasses offering customers an even wider range of product options. |
|
.jpg) |
|
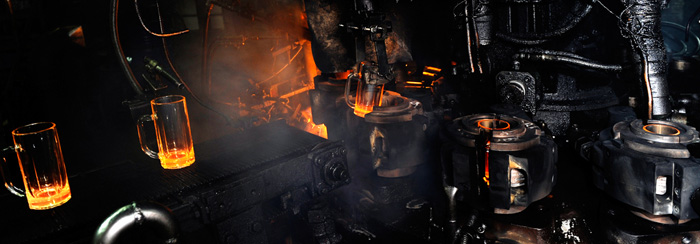 |
|
We acquired heat-resistant product technology for kitchenware glass from Japan's Sibata Hario and Germany's JSJ and E.P.T. Glass starting in 1987. We currently provide OEM and OD and services to well-known international household appliance and hardware assembly firms. We can fabricate molds with styling meeting customers' needs, and use high quality raw materials to produce acid/alkali-resistant products able to withstand heating to 150°C and above. We employ integrated kitchenware glass production processes, and blowing, molding, opening cutting, mouth compression, and printing are performed in a continuous process. This ensures product quality and allows us to maintain the highest level of customer satisfaction. |
|
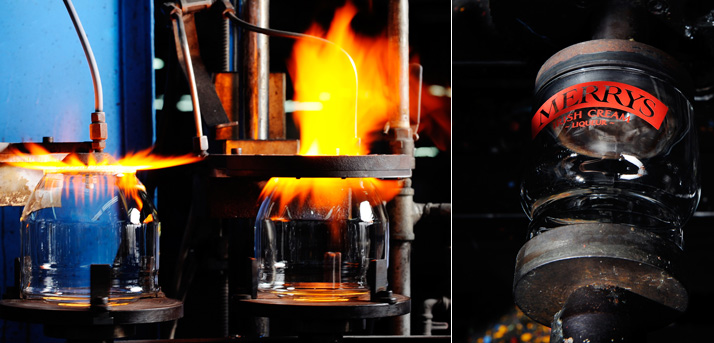 |
|
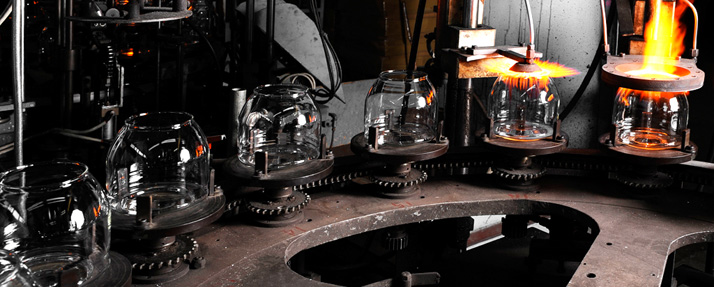 |
|
In addition, in order to boost product competitiveness, our Hsinchu plant has adopted computerized production, quality monitoring, and automated warehouse management. The plant has also passed ISO 9001 and ISO 14001 quality and environmental system certification. We are acquiring new production technology and our quality management system extends to all personnel. We are certain that our products will meet customers' requirements, helping us expand our market. |
|
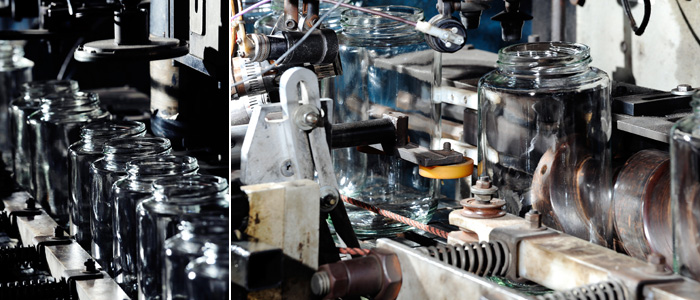 |
|
.jpg) |
|
In recent years, our Hsinchu plant has not only improved technology and developed many new products, but has also actively responded to the government's environmental protection, energy conservation, and carbon reduction policies. The plant's glass disposal facility has helped reduce the burden on the environment, and also provided industry with a good demonstration of how to conserve resources and protect the environment. Looking ahead to the future, Taiwan Glass's Hsinchu plant will persist in its ongoing R&D and production undertakings, and continue to provide customers with satisfying products and services meeting quality requirements even higher than those in the rest of the industry. |
|
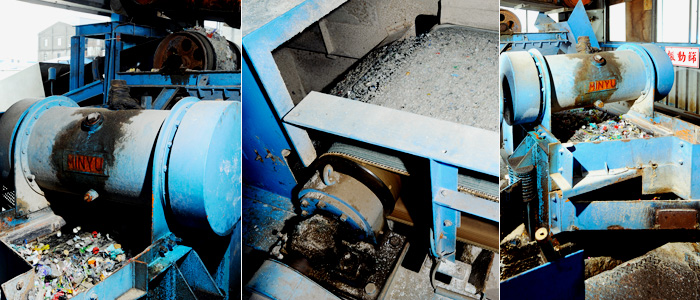 |
|
To better its quality service, Taiwan Glass’s Hsinchu Factory has invested NT$250 million in installing an automated storage and retrieval system (ASRS), taking the lead in the logistic management among glass industry in Taiwan. The well-controlled storage climatic environment enables the prevention of contamination and pest problems. The use of S.R.M.(Storage And Retrieval Machine) and conveyors largely reduces the need for fork lifters and meanwhile, packing stability increases considerably with low breakage rate and other relevant quality issues. |
|
ASRS is capable of providing customized and flexible-loading services, satisfying customers’ request for a mix of different products packed into one container. Generally, the system is efficient enough to load a 40-foot container within 20 minutes. In addition, “First In First Out” can be easily realized through computerized information management to assist customers in controlling the quality of inventories. |
|
The system meets HACCP standards on food grade packaging storage management and each pallet has its own barcode identification, verifiable through connecting to the logistic and quality traceability system at customers’ side. |
|
|
|
|
|